Contemporary Metalwork: Mapping Welding and Fabrication Trends for 2025
- David Fenton
- Feb 6
- 4 min read
In a world increasingly dependent on technology, how does a trade like welding stay relevant? As we look to the future, what kind of innovations can we expect in the field of welding and fabrication? And ultimately, how will these anticipated trends redefine the industry in 2025? A contemplation of these questions places us in the epicentre of a paradigm shift, where analogue trades are blending with digital innovation. Welcome to the exciting world of welding and fabrication in Brisbane, where technological advancements are becoming an integral part of the artistic and structural landscapes.
What, you may ask, is fuelling this transition? The answer lies in the developmental progress witnessed in various sectors. From monumental architecture to detailed art, the demand for intricate and advanced welding techniques is soaring. In this blog post, we delve into the future of welding and fabrication - a future where these techniques will be redefined by collaborative robotics, fibre laser technology, 3D printing, and more sustainable practices among other revolutionary trends.
As we gear up to explore these anticipated advancements in the niche of welding and fabrication, it's important to be aware that these innovations will not only redefine techniques but also impact economies, environments, education sectors and job scopes around the globe. Let's embark on this journey into the future, keeping an eye on the transformation that lies ahead.

The Uncharted Horizons of Collaborative Robotics:
Robotics has been a part of the fabrication industry for decades now, but the advent of collaborative robots, or "cobots," marks a new chapter. Cobots work in conjunction with humans, making the welding process safer and more efficient. Instead of replacing the human workforce, they amplify the potential of human craftsmanship, combining the precision and consistency of machine work with the creativity and critical thinking of a skilled tradesman.
Cobots are designed to co-exist in the working environment with humans. Unlike their traditional counterparts, they come in compact sizes and are flexible, easy to program, and affordable. These robots are equipped with sensors that make them sensitive to human proximity and thus, are vigilant enough to pause or slow down during critical operations.
The rise of cobots suggests a shift in the welding industry towards cooperation rather than replacement, a more holistic and enriched approach towards craft and creation. As we move closer to 2025, the integration of cobots will only increase, heralding a more human-centric approach to the fabrication industry.
From Traditional to Transformative - The Leap to Fibre Laser Technology
One of the key trends set to disrupt the welding industry is the shift from conventional to fibre laser technology. Fibre lasers are known for their incredible power efficiency, compact size, high beam quality, and reduced maintenance needs. But what makes them a game-changer in the world of welding?
Fibre lasers are known for their incredible speed and precision. They can weld at a high speed without causing damage to the surrounding areas, resulting in improved productivity and reduced waste. Their ability to adapt to different materials and thicknesses will greatly elevate the versatility of welding techniques in the near future.
As we move to 2025, fibre lasers will probably become commonplace in the welding industry. Not just for their efficiency and precision, but also because they signpost the way to a more sustainable and less wasteful approach to fabrication.

A Leap into the Third Dimension – 3D Printing and Welding
Imagine being able to create intricate 3D structures using welding techniques! This isn't a flight of fancy, but a very real possibility facilitated by 3D printing technology. An innovative technique known as "Wire Arc Additive Manufacturing," in which a metallic wire is melted and deposited layer by layer to create a 3D object, is set to redefine the boundaries of fabrication.
3D printing in welding allows the creation of complex shapes and structures, transforming a 2D sketch into a 3D reality. This can lead to a significant reduction in material wastage and time. As sustainability and efficiency become more crucial, 3D printing in welding is a trend closely aligned with these global objectives.
The increasing focus on bespoke design in art and architecture will further fuel the need for such innovative techniques. By 2025, we can reasonably expect to see the fusion of 3D printing and welding become central to fabrication practices across a variety of sectors.
Green Welding - The Future is Sustainable
As we contemplate a future where sustainability takes centre stage, how can the welding and fabrication industry align itself with this ethos? Well, the answer lies in the emerging trend of green welding. It involves recycling welding fumes and using welding machines that use less electrical consumption.
Green welding also embodies innovation in welding processes and materials. For instance, the use of friction stir welding can decrease energy consumption and reduce harmful emissions. These initiatives heavily underscore the industry's commitment to tread lightly on the planet.
Therefore, we head towards 2025 with a greater emphasis on sustainable welding practices which benefits not just the industry but the entire planet.
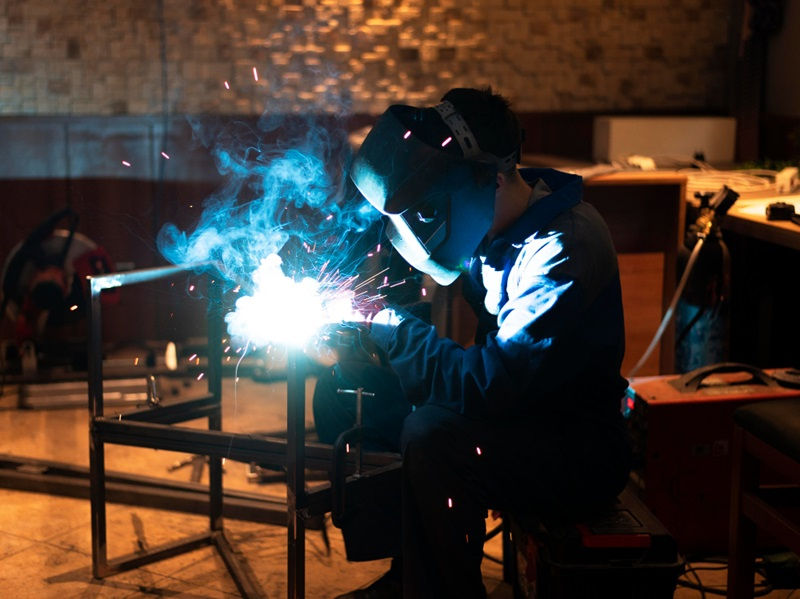
Conclusion: Sculpting the Future of Welding
As we chart the future trends of welding and fabrication, the narrative is tilting towards transformative technologies, human-machine collaboration, innovative methodologies, and sustainability. 3D printing unlocks the door to complex design possibilities, Cobots turn the age-old fear of technology replacing humans on its head, fibre lasers usher efficiency, and green welding grounds us in sustainable practices.
Each trend signals a step forward in not only technological advancement but reflects a broader commitment to sustainability and a human-centric approach. These aren’t just trends; they are markers of advancements that place equal focus on craft, creativity, and our collective responsibility towards the planet. As we turn the corner into a thrilling new era of welding and fabrication, the view to 2025 weaves technology with sustainability and human ingenuity, crafting a future that is as innovative as it is exciting.
Comments